Специалисты компании Bühler AG проводят тщательную проверку комплексов литья под давлением клиентов компании и демонстрируют способы повышения энергоэффективности.
Детали автомобилей все чаще изготавливаются не из стали, а из алюминия методом литья под давлением. Применение облегченных деталей способствует сокращению расхода топлива автомобилями и, следовательно, приводит и к сокращению выбросов углекислого газа (CO2).
Снижение массы транспортного средства на 100 кг позволяет сократить расход топлива на 0,4 литра на каждые 100 км пробега.
Обеспечение энергоэффективности становится всё более важной задачей, в том числе и для заводов, занимающихся литьем под давлением.
- Во-первых, к промышленным предприятиям предъявляются все более строгие требования в части обеспечения экологической устойчивости производства.
- Во-вторых, сокращение энергопотребления выгодно и с экономической точки зрения: «Для крупных литейных заводов затраты на энергетические ресурсы могут достигать нескольких миллионов евро в год», — говорит Мартин Лаглер, инженер-технолог Бюлер.
В целях повышения энергоэффективности комплексов литья под давлением компания Бюлер предлагает специализированные консультационные услуги: «Мы проводим детальные измерения технологических параметров, рассматриваем процессы литья под давлением в целом и демонстрируем нашим клиентам различные возможности оптимизации их производств», — поясняет Лаглер. На типовом литейном заводе более половины энергопотребления (54%) приходится на плавильные печи. Следующим по величине потребителем является инфраструктура здания, на которую приходится 34% энергозатрат. Сам же комплекс литья под давлением потребляет лишь 12% от общего количества расходуемой энергии.
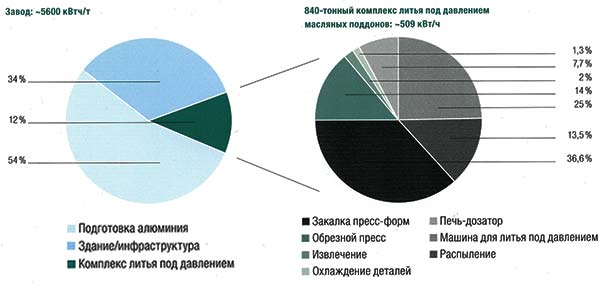
Рис. 1: Диаграмма энергопотребления типичного завода литья под давлением
Повышение качества и предотвращение потерь
«Ключом к устойчивому сокращению энергопотребления является оптимизация технологического процесса в целом: даже незначительные усовершенствования, повышающие общую эффективность оборудования (англ. — Overall Equipment Effectiveness, ОЕЕ), приводят к сокращению операционных расходов и энергопотребления для каждой изготавливаемой детали», — говорит Лаглер.
К ключевым факторам успеха относятся повышение качества продукции и сокращение объема брака. Ведь бракованный блок не только не может быть продан, но и подлежит переплавке. Следовательно, любой брак приводит к нарушению энергетического баланса. Огромные возможности в части экономии ресурсов и средств связаны также с сокращением длительности производственного цикла: «Сокращение времени изготовления блока двигателя со 120 до 90 секунд приводит к значительному сокращению затрат энергии на единицу производимой продукции», — поясняет Лаглер. При этом, также важно минимизировать время простоя оборудования. Даже если в какой-то момент времени производство остановлено, сохраняется базисная энергетическая нагрузка на комплекс литья под давлением.
«Наш Анализатор событий (Event Analyzer) — это программный инструмент для анализа остановок литейных комплексов. Он позволяет выявлять и устранять конкретные неисправности, повышая при этом эксплуатационную надежность установки», — говорит Лаглер.
Повышение эффективности машин
Рабочие характеристики машин также могут быть усовершенствованы: в качестве привода используется мощный электродвигатель, управляющий всеми движениями машины посредством гидравлической системы. «Применение эффективных гидравлических и приводных систем позволяет сэкономить до 20% затрачиваемой энергии», — говорит Лаглер.
Крупные потребители энергии также оснащаются блоками регулирования температуры, обеспечивающими поддержание температуры пресс-формы, а также распылителями для нанесения разделительного покрытия и охлаждения пресс-форм при помощи сжатого воздуха. «Интеграция системы охлаждения пресс-формы позволяет значительно сократить расход сжатого воздуха, тем самым сокращая затраты энергии на распыление (до 90%) и в то же время сокращая длительность производственного цикла», — поясняет Лаглер.
Cпециалисты компании Бюлер часто распознают потенциальные возможности для оптимизации в самых неожиданных местах. Так, например, специалисты заметили, что при транспортировке от плавильной печи до комплекса литья под давлением температура расплавленного алюминия зачастую опускается ниже заданной, вследствие чего требуется повторный нагрев металла в печи для выдержки. Это приводит к значительным затратам энергии и снижению эффективности процесса. «Нам удалось найти решение этой проблемы — в данном случае это была оптимизация маршрута вилочных погрузчиков, перевозящих жидкий металл к литейным комплексам», — рассказывает Лаглер. Инженеры-технологи часто находят способы усовершенствовать процесс там, где такие возможности, на первый взгляд, вовсе не очевидны. «Именно поэтому нам важно иметь возможность получить взгляд на процесс со стороны», — подводит итог Лаглер.
Контактное лицо для получения более подробной информации:
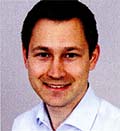
Мартин Лаглер
Инженер-технолог Подразделения
прикладных технологий
Бюлер АГ, Уцвиль
Телефон: +41 71 955 13 75
E-mail: martin.lagler@buhlergroup.com
http:// www.buhlergroup.com
Контакты в Украине
Представительство Бюлер АГ в Украине
Украина, 02098, г. Киев,
ул. Шумского Ю., д. 1А, офис 118
Телефон/Факс: +38 (044) 520-55-85
E-mail: vira.derii@buhlergroup.com
http:// www.buhlergroup.com
Tags:
Литье под давлением