В литье по выплавляемым моделям из алюминиевых сплавов для каждой детали, которая должна быть изготовлена из расплавленного алюминия, должна быть изготовлена одноразовая модель из воска. Чтобы изготовить указанные модели из воска, низкотемпературный пастообразный воск впрыскивают в пресс-формы. Для того, чтобы получить высокий — образец качества, полость пресс-формы должна быть полностью заполнена, так чтобы воздух не оставался в пресс-форме, что будет создавать пузырь или пустоту в окончательной схеме. Поэтому поток пастообразного воска должен контролироваться, чтобы захваченный воздух мог выходить через вентиляционные отверстия в пресс-форме.
Проблемы, с которыми это связано, хорошо известны инженерам Solidiform Inc. из Форт-Уэрта (шт. Техас, США) — лидера в производстве алюминиевых отливок по выплавляемым моделям и прецизионных песчаных отливок для аэрокосмической промышленности. Компания недавно модернизировала свою систему впрыска воска и получила несколько запросов от инженеров, работающих над обновлением.
«Когда пресс-форма была почти заполнена, мы хотели, чтобы машина замедляла скорость заполнения, чтобы позволить воздуху выходить», — говорит вице-президент и генеральный директор Solidiform Ларри Андре. «Проблема с нашим старым восковым экструдером заключалась в том, что мы не могли вручную изменять скорость потока во время впрыска, поэтому мы были вынуждены выбрать компромиссную скорость заполнения».
В результате в пресс-форме часто оставалось некоторое количество воздуха, что создавало пустоты в восковой моделе, которые необходимо было отремонтировать, прежде чем модель можно было использовать на следующей стадии процесса.
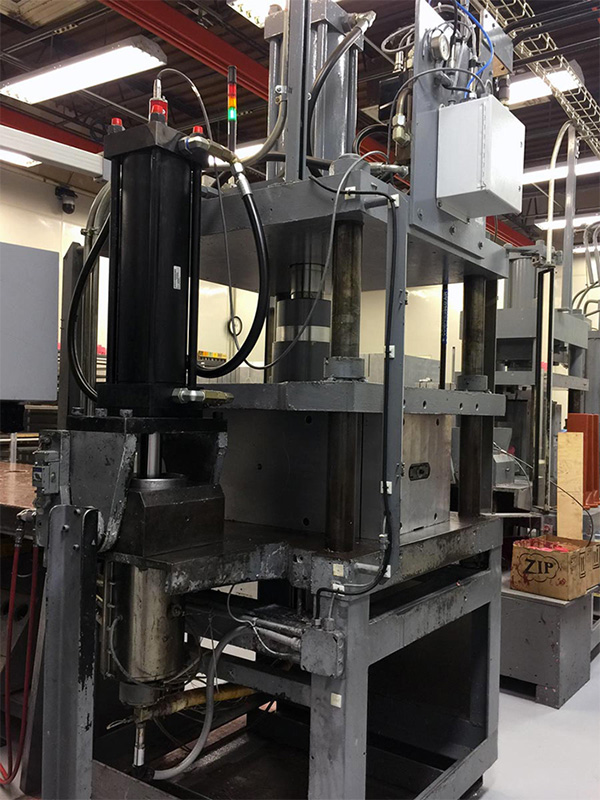
Рис. 1: Черный цилиндр (вверху слева) сжимает горячий воск. Цилиндр (вверху по центру) зажимает форму, закрытую на сопле впрыска на неподвижной плите
Автоматизация операции
Чтобы избежать повторной обработки и сделать процесс более повторяемым, руководство Solidiform искало способ контролировать, как воск заполняет форму. Было предпринято несколько решений, включая клапаны с ручным управлением расходом и регуляторы давления с электронным управлением, но все они имели ограниченный успех. Чтобы решить эту проблему, они связались с компанией Wilson, дистрибьютором гидравлической энергии по всему Техасу со штаб-квартирой в Аддисоне.
Инженер Wilson Дэйв Пеллерен (Dave Pellerin) порекомендовал, чтобы электрогидравлический контроллер движения для цилиндра, в котором работает восковой экструдер, давал им точное управление. Пеллерен рекомендовал Solidiform использовать RMC75E от Delta Computer Systems, Inc., Батл-Граунд, Вашингтон.
В начале процесса восковая заготовка загружается в цилиндр экструдера с температурой, поддерживаемой нагревательными лентами снаружи. Затем цилиндр экструдера проталкивает теплый воск через нагретый шланг, чтобы заполнить форму, которая удерживается закрытой зажимным цилиндром. Контроллер движения использует заданные значения, введенные из базы данных для скорости впрыска и давления, чтобы обеспечить постоянное заполнение.
Сжимаемость воска отличается от сжимаемости воздуха, и система управления контролирует и регулирует это путем считывания выходного сигнала датчика давления в линии воска. Используя эту информацию, давление впрыска может динамически изменяться по мере заполнения формы.
Контроллер реагирует на изменения давления, увеличивая или уменьшая свою команду для сервоклапана. Как только воздух удаляется, давление почти сразу же возвращается. К этому времени контроллер должен быстро реагировать, снижая управляющее напряжение до соответствующего уровня (и, следовательно, уменьшая поток гидравлической жидкости в цилиндр инжектора), чтобы минимизировать перерегулирование. Контроллер движения также компенсирует разницу вязкости воска от одного производственного цикла к другому. Контроллер обеспечивает точность и повторяемость заданного давления от выстрела к выстрелу.
Контроллер движения Delta контролирует давление и положение поршня в каждом цилиндре. Используемый алгоритм управления называется «двухконтурным управлением». Внутренний контур управления обеспечивает, чтобы положение и скорость поршня соответствовали профилю при впрыскивании воска, тогда как внешний контур проверяет, что давление, действующее при перемещении поршня, не превышает установленные пределы.
Все функции впрыска координируются с помощью сенсорного экрана Red Lion, основного интерфейса оператора. Интерфейс HMI также взаимодействует с ПЛК Allen-Bradley, который контролирует последовательность силового блока и механизмы безопасности.
После завершения цикла впрыска RMC75E создает небольшое отрицательное давление в восковой линии при втягивании зажимного цилиндра. Это гарантирует, что остаточный воск не выплескивается при снятии давления зажима. Все значения давления отображаются в HMI.
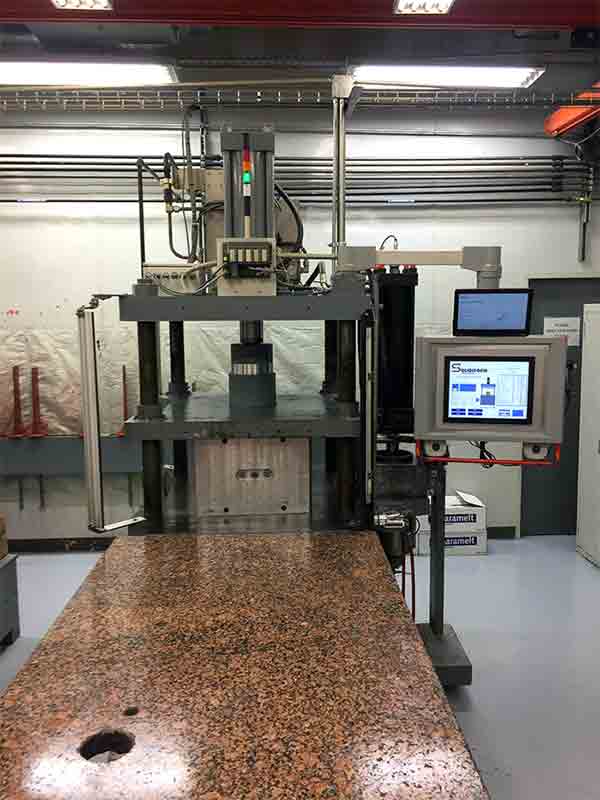
Рис. 2: Работа пресса контролируется на панели управления Red Lion. Все функции впрыска координируются с помощью сенсорного экрана, основного интерфейса оператора
Программирование движения
Чтобы упростить настройку параметров движения, Delta предоставляет программный инструмент Plot Manager, являющийся частью программного интерфейса компании RMCTools. Графики, созданные этим модулем, отображают значения фактических параметров движения, а не целевые значения, рассчитанные алгоритмом контура управления. Графики позволяют им наметить ожидаемые действия, такие как:
- Время от 0 до 10 сек .: вводится воск. В пресс-форме слишком много воздуха, чтобы считывать обратное давление.
- Через 10 сек .: быстрый удар давления. Форма начинает заполняться, поэтому давление измеряется. Тем не менее, он быстро рассеивается, когда появляется захваченный воздушный пузырь.
- В 10,75 сек .: резкое повышение давления по мере выталкивания последнего воздуха и заполнения формы. Напряжение управляющей команды слишком высокое, потому что показания не являются реальными, но контроллер быстро реагирует на устойчивый выходной сигнал. После того, как весь воздух вытеснен и форма полностью заполнена воском, на это уходит примерно 0,1 секунды. для повышения давления воска в форме.
- В 11 сек .: Давление начинает стабилизироваться и поддерживается на заданном уровне в течение всего цикла, позволяя воску затвердеть под давлением.
Графики, подобные этим, можно использовать для диагностики проблем с движением. Например, перед окончательной настройкой графики показали некоторую вибрацию в системе (колебания в положении цилиндра). Это было вызвано тем, что экструдер переходил от впрыскивания воска к попаданию захваченного воздушного пузыря. Для решения проблем была вызвана команда поддержки Delta, которая порекомендовала некоторые настройки системы, которые использовали быстрое время цикла контроллеров и расширенные параметры настройки, а также добавили выходной фильтр нижних частот, который настроил эти колебания.
«Теперь контроллер Delta может дать нам переменную скорость потока, адаптированную к той части, которую мы хотим создать», — говорит Андре. «И это может поддерживать давление точно и многократно, нет никаких догадок. Контролируя скорость заполнения пресс-формы и не допуская образования дефектов, мы легко увеличили наш первый выход шаблона и нам не нужно делать никаких ремонтов. Мы, вероятно, увеличили производительность на 20% ».
Автор
Jason Palmer (Джейсон Палмер) — региональный инженер по приложениям в Delta Computer Systems Inc., телефон: +1 360-254-8688, https://deltamotion.com. Delta Computer Systems разрабатывает и производит электрогидравлические контроллеры движения с приложениями по всему миру.
Источник: www.machinedesign.com
Tags:
ЛВМ