Задолго до многих современных технологических достижений у людей были термически обработанные металлы, чтобы улучшить их физические и химические свойства для конкретного применения. В средние века кузнецы ковали и отпускали металлы (хотя и довольно грубо) для создания лезвий, инструментов и товаров для повседневной жизни. В настоящее время металлурги и инженеры-металловеды имеют гораздо более широкий спектр специализированных методов и оборудования для адаптации материалов к конкретным применениям.
Существует множество видов термической обработки, таких как закалка, отпуск, старение, снятие напряжения и поверхностная закалка. Чтобы избежать путаницы, рассмотрим наиболее распространенные термические обработки, а также их цели и их плюсы и минусы.
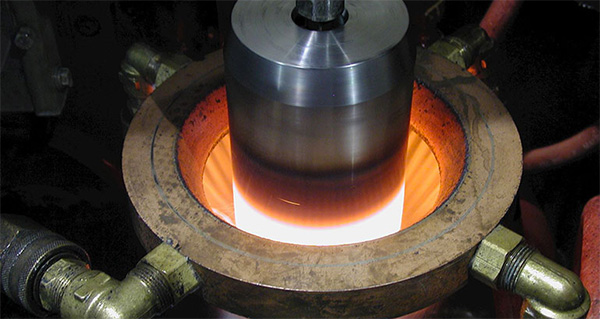
Рис. 1: Этот вал подвергается индукционной закалке. Локальный нагрев на валу (красное / белое свечение) немедленно сопровождается закалкой распыленной водой, которая быстро охлаждает его
Отжиг
Отжиг включает повышение температуры металла до тех пор, пока он не окажется в равновесном состоянии, как это определено его фазовой диаграммой. Он используется для изменения физических свойств металла, таких как его твердость, но также могут быть локальные химические изменения, в зависимости от фазовых переходов. Процессы отжига обычно следуют за обработкой, такой как механическая обработка и шлифование, или даже другими термообработками, такими как закалка.
Закалка и отпуск. Закалка включает нагрев стали выше ее критической температуры и достаточно длительную выдержку при данной температуре, чтобы позволить микроструктуре полностью перейти в аустенитную фазу. Сталь затем охлаждают, процесс, который быстро охлаждает сталь, помещая ее в воду, масло или раствор полимера. Это «замораживает» его микроструктуру. То, что сталь подвергается закалке для охлаждения, контролирует скорость охлаждения, а скорость охлаждения определяет микроструктуру после закалки.
Металлурги используют диаграмму изотермического превращения (аустенита) время — температура — превращение (диаграмма TTT), чтобы предсказать результирующую микроструктуру, будь то мартенсит, бейнит или перлит. Черные сплавы с содержанием углерода больше чем 0,3 мас.%, могут быть чрезвычайно твердым (> 60 HRC), особенно мартенситная структура. Но повышенная твердость сопровождается снижением прочности.
После закалки сталь становится чрезвычайно твердой и хрупкой, поэтому она подвергается еще одному шагу, чтобы уменьшить ее твердость и повысить ее пластичность, сохраняя при этом свою микроструктуру.
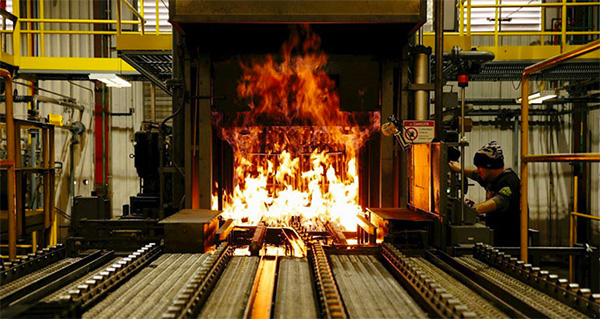
Рис. 2: Металлические детали загружаются в корзины, а затем вытягиваются в цементационную печь в Advanced Heat Treat Corp. Там они нагреваются выше критических температур металла
Закалка стали ниже ее критической температуры позволяет ей сохранять свою мартенситную структуру, но, если ее выдерживать достаточно долго, она превращается в смесь феррита и небольших карбидов, точный размер которых зависит от температуры отпуска. Это делает сталь более мягкой и пластичной. Основными параметрами отпуска являются температура и время, и они должны точно контролироваться для создания желаемой конечной твердости. Более низкие температуры поддерживают более высокую твердость при снятии внутренних напряжений, а более высокие температуры снижают твердость.
После первоначального литья или механической обработки закалка и отпуск придают стали твердость и прочность для изготовления деталей с характеристиками материала. Затем детали могут быть обработаны до конечного состояния. Закалка и отпуск деформируют металл, поэтому детали всегда проходят эти два процесса перед окончательной обработкой. Для деталей с дополнительными процессами термообработки, используемыми для изменения свойств поверхности, закалка и отпуск определяют основные свойства детали, такие как твердость, прочность и пластичность. (Дополнительные процедуры поверхностного упрочнения будут рассмотрены позже.)
Снятие напряжений. Снятие напряжения — этап отжига, следует за шлифовкой, холодной обработкой, сваркой или окончательной обработкой и выполняется после того, как металл был закален и отпущен до желаемой микроструктуры и прочности. Это означает, что особое внимание следует уделить тому, чтобы заготовка не отжигалась слишком близко к ее температуре отпуска. Это предотвращает изменение ранее достигнутой твердости и микроструктуры.
Снятие напряжения удаляет внутренние дислокации или дефекты, делая металл более стабильным по размерам после окончательной обработки, такой как азотирование газом или ионами. Снятие напряжения не предназначено для значительного изменения физических свойств металла; изменения твердости и прочности фактически нежелательны.
Дисперсионное упрочнение. Дисперсионное упрочнение — это особая стадия отжига, также известная как искусственное старение из-за того, что некоторые металлы со временем затвердевают при докритических температурах. Как уже отмечалось, этот метод упрочнения металлов ограничен теми, которые подверглись закалке и являются перенасыщенным раствором, что означает, что материал находится в неравновесном состоянии по отношению к присутствующим фазам.
В этих сплавах перенасыщенный раствор мартенсита нагревают (от 500 до 550°С) и выдерживают в течение от 1 до 4 часов, позволяя выделяющейся фазе равномерно образовываться и расти. Это приводит к получению неискаженной стали с высоким пределом текучести и с лучшими износостойкими свойствами, чем в ее неизменном состоянии. Состав и размеры фазы зависят от возраста сплава, но все они имеют одинаковый общий эффект упрочнения материала.
Не все железные сплавы имеют право на этот механизм закалки, но мартенситные нержавеющие стали, такие как 17-4, 15-5 и 13-8, являются отличными кандидатами, а также стали для фрезерования. (Термин «maraging» сочетает в себе два слова «мартенситный» и «старение». Эти стали имеют превосходную прочность и ударную вязкость без потери пластичности, но они не могут удерживать хорошую режущую кромку. Старение относится к длительному процессу термообработки.) В этих сплавах перенасыщенный раствор мартенсита нагревают (от 500 до 550°С) и выдерживают в течение от 1 до 4 часов, позволяя
выпадению новой фазы из пересыщенного твердого раствора, ее равномерному образованию и росту. Это приводит к получению неискаженной стали с высоким пределом текучести и пределом текучести с лучшими износостойкими свойствами, чем в ее неизменном состоянии.
Индукционная закалка очень похожа на закалку, с одним отличительным отличием: нагрев при индукционной закалке избирательный. Это связано с тем, что при индукционной закалке нагрев осуществляется с помощью магнитных катушек, которые соответствуют геометрии детали. Это означает, что критические характеристики детали могут быть усилены, а ядро детали — нет. Вместо этого сердечник сохраняет прочность и пластичность металла. Эта операция выполняется с использованием воды, масла или раствора полимера.
Индукционная закалка может выполняться на сталях с содержанием углерода более 0,3 мас.% и на деталях с размерами и геометрией, для которых могут быть разработаны индукционные катушки. Индукционная закалка также значительно сокращает время обработки, необходимое для упрочнения деталей, и снижает риск обезуглероживания. В отличие от традиционного нагрева и закалки, индукция представляет собой поверхностную термообработку с закаленной глубиной от 0,5 до 10 мм.
Поверхностная закалка
Термическая обработка с закалкой, которая включает азотирование, нитроуглероживание, цементацию и карбонитрирование, изменяет химический состав детали — в отличие от ранее упомянутых методов отжига — и фокусируется на свойствах ее поверхности. Эти процессы создают закаленные поверхностные слои глубиной от 0,01 до 0,25 дюйма, в зависимости от времени обработки и температуры. Увеличение толщины затвердевшего слоя сопряжено с более высокими затратами из-за дополнительного времени обработки, но увеличенный срок службы детали может быстро оправдать дополнительные затраты на обработку. Специалисты по материалам могут применять эти процессы для обеспечения наиболее экономически эффективных деталей для конкретных применений.
Науглероживание и карбонитрирование. Науглероживание идеально подходит для деталей, требующих дополнительного упрочнения на поверхности для износостойкости, но для более высокой прочности требуется более мягкое ядро. Науглероживание — это высокотемпературный процесс (от 900 до 950° C), который включает добавление и диффузию углерода в сталь. Эти температуры превышают критическую температуру стали, поэтому последующее охлаждение позволяет обогащенной углеродом поверхности образовывать мартенсит, в то время как ядро остается более мягкой структурой феррита и / или перлита. Глубина закаливания может составлять 0,25 дюйма, в зависимости от того, сколько времени деталь выдерживает при температуре цементации.
Как уже упоминалось, преимуществом науглероживания является глубокий износостойкий слой с высокой твердостью. Это идеально подходит для зубчатых колес, лезвий и режущих инструментов. Науглероживание создает твердые, долговечные детали из более дешевых легированных сталей и низкоуглеродистых сталей, таких как 1008, 1018 и 8620. Для сплавов с более высоким содержанием углерода (> 0,3 мас.% углерода) науглероживание оказывает минимальное или даже вредное воздействие, поскольку углерод в оригинальный сплав может привести к сквозной или объемной структуре мартенсита. Следует также отметить, что температуры науглероживания вызывают некоторые искажения.
Для низкоуглеродистых сталей без значительного количества легирующих элементов, способствующих упрочнению, добавление азота в процесс может повысить твердость поверхности. Добавление азота называется карбонитрированием. Карбонитрирование обычно выполняется при несколько более низких температурах, чем науглероживание (850°C), поэтому искажения меньше, но это также уменьшает глубину закалки (для сопоставимого времени обработки). Закаленная поверхность, созданная во время карбонитрирования, хотя и более тонкая, обладает большей твердостью и устойчивостью к повышенным температурам обработки (таким как отпуск и снятие напряжения).
Азотирование и нитрокарбонизация. Альтернативой высокотемпературному науглероживанию / карбонитрированию является азотирование / нитрокарбюризация. Он также производит упрочненные поверхностные слои и аналогичные износостойкие материалы, но рассеивает азот по всему поверхностному слою (не углерод) и использует докритические температуры обработки. Типичные температурные интервалы для азотирования составляют от 450° до 575°С. Это означает, что детали могут быть обработаны в их окончательном обработанном состоянии и практически не подвержены искажениям, поэтому требуется небольшая обработка после азотирования (если таковая имеется). Более низкие температуры также поддерживают желаемую микроструктуру ядра и физические свойства, изменяя поверхностный слой для данного применения. Одно замечание, которое следует учитывать при выборе азотирования: Проинформируйте термообработчика о любых температурах снятия напряжения, старения или отпуска, чтобы предотвратить изменение свойств активной зоны.
В отличие от науглероживания, которое ограничивается сталями с низким содержанием углерода, широкому диапазону сплавов может быть придана твердость поверхности от 600 до 1200 Hv посредством азотирования. Но сплавы, лучше всего подходящие для азотирования, обычно содержат номинальные количества микролегирующих элементов: Cr, V, Ti, Al и Мо. Азотирование может быть чрезвычайно полезным для нержавеющих и инструментальных сталей, содержащих большие количества хрома (10 + мас.%). Эти азотированные стали могут иметь твердость поверхности, значительно превышающую 70 HRC-эквивалентов, идеально подходящую для долговременной износостойкости.
Азотирование также не ограничивается этими типами черных сплавов, так как низкоуглеродистые стали также могут быть закалены. Помимо создания закаленной, износостойкой поверхности, азотирование также образует составную зону. Составные зоны представляют собой слои, богатые азотом, которые образуются на поверхности во время азотирования, которые являются твердыми, износостойкими (эквивалент> 60 HRC) и устойчивыми к коррозии. Это выгодно для низкоуглеродистых и низколегированных сталей, которые не учитывались бы в суровых условиях окружающей среды, если бы не наличие сложной зоны.
Глубина закалки для азотированных / нитроуглеродистых сплавов обычно составляет от 0,005 до 0,030 дюйма, в зависимости от времени и температуры процесса. Более глубокие отвержденные слои требуют больше времени. Толщина составной зоны может составлять до 0,002 дюйма. толщиной, и это зависит от того, какой сплав нитридов, время и температура. Способ азотирования детали также влияет на глубину зоны. Азотирование может осуществляться с помощью газа или иона (плазмы).
В газообразном азотировании в качестве источника азота используется крекинг-аммиак, и это происходит в среде с положительным давлением. Он идеально подходит для пакетной обработки большого количества, а также превосходен в отношении однородности температуры и азотирования деталей с глубокими отверстиями или каналами. Азотирование азотом не рекомендуется для пористых деталей, поскольку газ, проходящий через поры, может вызвать сильное охрупчивание.
Ионное азотирование отлично подходит для селективного азотирования, поскольку детали могут быть замаскированы от плазмы для предотвращения азотирования. Ионное азотирование выполняется путем приложения разности потенциалов между анодом и деталью (катодом) в вакууме. Эта разность потенциалов образует азотную плазму (уникальное пурпурное свечение), которая заставляет атомы азота попадать на открытые поверхности детали.
Плазменное азотирование хорошо подходит для сплавов, таких как нержавеющая сталь, поскольку оно быстро разрушает пассивные оксидные поверхности. Как правило, ионно-азотированные стали имеют более тонкие составные зоны, чем их газо-азотированные аналоги из-за постоянного распыления плазмы. Но это может быть идеальным для определенных применений, таких как зубчатые колеса, где контактные напряжения могут повредить поверхности с чрезмерно сложными зонами.
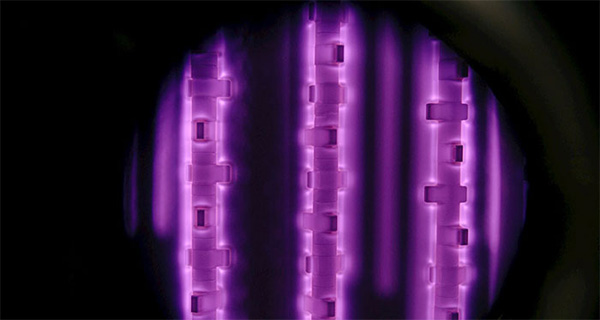
Рис. 3: Пурпурное свечение окружает эти части азотированными ионами (плазмой). Это вызвано ионизированными и возбужденными молекулами и атомами азота, бомбардирующими поверхность детали из-за приложенного потенциала. Только поверхности, подвергаемые воздействию плазмы, азотированы
При сравнении азотирования и нитроуглероживания последнее обычно выполняется при более высоких температурах (575°C) и используется источник углерода. Добавление углерода образует более твердый, более износостойкий и более смазывающий слой. Более толстые составные зоны также могут образовываться путем нитроуглероживания. Для сравнения, среда для азотирования чистого азота образует твердый и износостойкий слой, но в меньшей степени, чем нитроуглероживающийся. Так почему же не всегда вводить использование нитрокарбюризации? Введение углерода может увеличить пористость поверхности, что плохо для деталей с большими контактными напряжениями. Полученный слой также менее пластичный.
Выбор материала также определяет, какие методы обработки лучше всего подходят для применения.
Это общее руководство объясняет множество термических обработок. Но при рассмотрении термической обработки инженерам важно помнить о следующих вопросах, касающихся конструкции их деталей: каким силам подвергаются мои детали? В какой среде они работают? Требует ли приложение определенных свойств для поверхности, ядра или определенных областей поверхности? Ответ будет направлять выбор.
Авторы
-
-
- Rich Johnson (Рич Джонсон) — менеджер материалы и процессы Advanced Heat Treat Corp.
- Edward Rolinski (Эдвард Rolinski) — научный сотрудник Advanced Heat Treat Corp.
- Mike Woods (Майк Вудс) — президент Advanced Heat Treat Corp.
-
Телефон: 319-232-5221.
Источник: www.machinedesign.com
Tags:
Термообработка