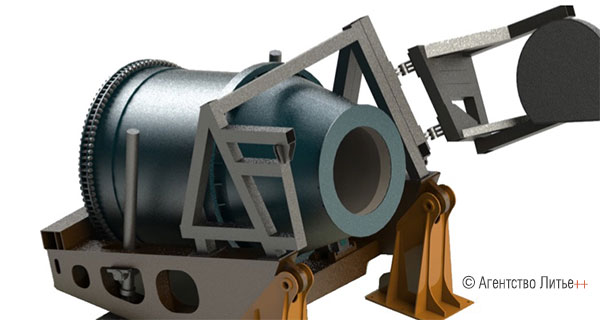
Рис. 1: Ротационная печь с наклоняемой осью вращения
Мировое производство вторичных алюминиевых сплавов в последнее десятилетие демонстрирует стабильный рост. Переработка лома и отходов алюминия — ключевой процесс в алюминиевой индустрии поскольку при этом экономится до 95% энергии требуемой для производства первичного алюминия.
В переработке алюминиевого лома основным процессом является плавка подготовленного сырья. Выбор плавильного агрегата существенно влияет на экономические показатели и на качество полученных сплавов. В табл. 1 представлены усредненные показатели потребления энергии плавильными агрегатами различной конструкции.
Таблица 1: Затраты энергии на расплавление алюминиевого лома в различных плавильных агрегатах
Тип плавильного агрегата | Количество энергии требуемое для расплавления 1 т алюминиевого лома |
Расчетное количество энергии (КПД=100%) | 310 кВт*ч |
Отражательная печь ванного типа | 1280 кВт*ч |
Шахтная печь | 630 кВт*ч |
Ротационная печь со стационарной осью вращения | 1000 кВт*ч |
Ротационная печь с наклоняемой осью вращения | 550 кВт*ч |
На сегодняшний день в мировой практике для металлургической переработки лома алюминиевых сплавов во вторичные марочные алюминиевые сплавы наиболее востребованы ротационные печи с наклоняемой осью вращения (tilting rotary furnace), которые обладают рядом важных достоинств, способствующих высокоэффективному ведению производства:
- Низкое потребление топлива (см. табл. 1).
- Высокое извлечение металла.
- Высокая производительность.
- Возможность работать на сильно засоренной и неподготовленной шихте, включая шлаки.
- Возможность автоматизации процесса.
В Северной Америке, Европе и, в частности, в Турции хорошо отработана технологическая схема производства, включающая следующий комплекс технологического оборудования участка переработки лома:
- Ротационная газовая плавильная печь с наклоняемой осью вращения — для переплава лома и отходов алюминиевых сплавов.
- Копильник (миксер) — для проведения рафинирования выплавленного сплава (дегазация, удаление неметаллических включений, вредных примесей и т.д.) и микролегирования. Миксер может быть как в газовом, так и в электрическом исполнении. Современные модели предполагают наличие механического ротора для перемешивания расплава, что существенно улучшает эффективность рафинирования расплава и скорость ввода легирующих элементов.
- Разливочный конвейер — для разливки марочного сплава в чушки.
Основной компонет комплекса — газовая ротационная печь (см. рис. 1), которая выполняет следующие технологические операции: загрузка печи, плавление, слив алюминиевого сплава, слив шлака, очистка футеровки печи от настылей и шлака (см. рис. 2). Емкость печей подобного типа обычно варьируется в диапазоне от 1 до 21 тонны. В табл. 2, в качестве примера, приводим основные характеристики печи средней емкости (5000 кг).
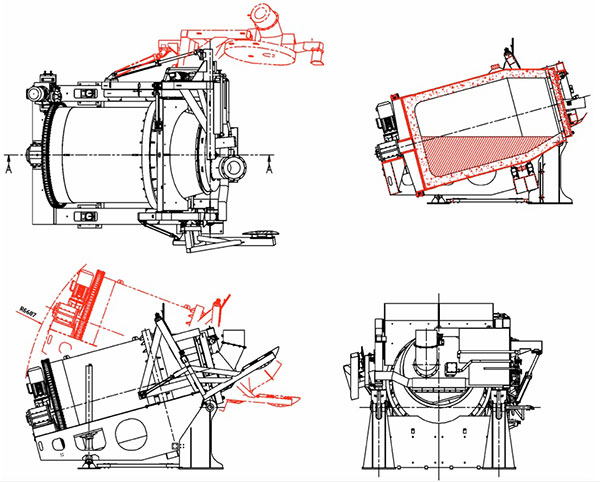
Рис. 2: Технологическая схема работы ротационной печи с наклоняемой осью
Таблица 2: Технические характеристики роторной печи с наклоняемой осью мод. ARTF-5
Наименование показателя | Величина показателя |
Вместимость | |
1. Вместимость по алюминию, кг | 5000 |
2. Диаметр загрузочного окна, мм | 1400 |
3. Рабочий объем, м3 | 2,5 |
4. Максимальный вес загрузки (включая флюс), кг | 5750 |
Производительность | |
5. Скорость плавки полной садки (п. 1), ч | ~2 |
6. Время технологических операций (загрузка шихты, слив расплава, выгрузка шлака), ч | ~1 |
7. Продолжительность цикла плавки (от выпуска расплава, до выпуска расплава), ч | ~3 |
8. Количество циклов плавки в сутки | 7-8 |
9. Максимальная производительность, т/месяц | 800 |
Горелочный блок | |
10. Минимальная мощность горелки, кВт | 372,1 |
11. Максимальная мощность горелки, кВт | 1860 |
12. Минимальное потребление газа, м3/ч | 38,8 |
13. Максимальное потребление газа, м3/ч | 193,9 |
14. Вентилятор, м3/ч | 2500 |
Привод барабана | |
15. Мощность привода вращения, кВт / В | 30 / 380 |
16. Угол наклона оси вращения, ° | 0-15 |
17. Скорость вращения барабана, об./мин. | 0-6 |
18. Номинальная производительность фильтрующего элемента, нм3/ч | 30 |
Гидравлическая система | |
19. Мощность привода гидростанции, кВт/В | 11 / 380; 60 Hz – IP-54 |
20. Наклон барабана печи осуществляется с помощью | 4-х гидроцилиндров |
Наши специалисты готовы проконсультировать заинтересованные компании по особенностям технологии переработки лома и отходов алюминиевых, цинковых, медных и свинцовых сплавов; подобрать и поставить комплексы или отдельные компоненты технологического оборудования для металлургической переработки лома и отходов цветных сплавов.
Авторы
СЕЗОНЕНКО Антон Юрьевич — к.ф-м.н., директор ООО «Инженерная компания — САС», г. Киев, телефон: +38 (044) 424-25-03, +38 (044) 423-82-99; e-mail: info@sasua.com.ua
СЕЗОНЕНКО Юрий Дмитриевич — технический директор ООО «Инженерная компания — САС», г. Киев, телефон: +38 (044) 424-25-03, +38 (044) 423-82-99; e-mail: info@sasua.com.ua
Tags:
Печестроение