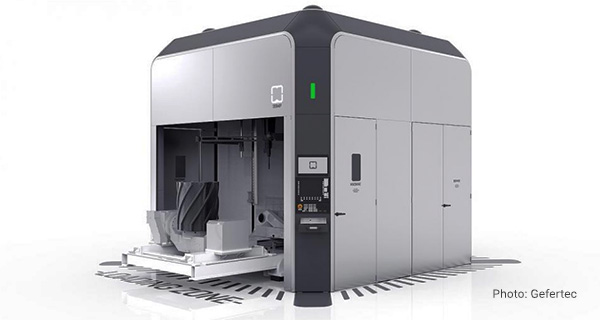
Рис. 1: Крышка подшипника колесной пары весом 11,5 кг была напечатана на машине Gefertec arc605
Поиск трудно заменяемых деталей создает новый аргумент в пользу 3D-печати. Несмотря на то, что литейные цехи продолжают полагаться на надежность своих конструкций и качество своей продукции, проблема, связанная с металлическими деталями с 3D-печатью, также связана с обслуживанием — доступностью определенного компонента по графику, который подходит заказчику. Таким образом, в то время как мировой железнодорожный рынок продолжает требовать тонны литых деталей каждый год, наличие локомотивов, железнодорожных вагонов и железнодорожных составов имеет критически важное значение с точки зрения надежности железнодорожных перевозок. И это открытие для альтернативы.
В Deutsche Bahn AG работают более 7000 человек, которые обслуживают несколько тысяч автомобилей, что доказывает, что приобретение и хранение запасных частей сопряжены с серьезными проблемами. 3D печать становится значительным преимуществом в поиске труднодоступных запасных частей. В последнее время Deutsche Bahn прибегали к Gefertec 3DMP ® процесса в рамках пилотного проекта по улучшению его сорсинг.
«Доступность является большой проблемой для нашей компании», — сказала доктор Тина Шлингманн, инженер по материалам, которая начала исследовать потенциальные приложения для производства добавок в Deutsche Bahn в прошлом году. Она указала, что металл AM важен не только для создания прототипов и оснастки, но и для бизнеса запасных частей.
Deutsche Bahn покупает поезда и локомотивы, а затем занимается техническим обслуживанием автомобилей на месте. Одной из проблем при обслуживании тысяч транспортных средств является то, что старые локомотивы ставят перед обслуживающими бригадами задачу получения запчастей, которые больше не поставляются производителями.
Крышка подшипника колесной пары
В последние годы Deutsche Bahn исследовал возможности аддитивного производства в более чем 100 областях применения. По словам Шлингманна, «детали, связанные с доступностью» были особенно важны для их исследований.
Недавний случай касался крышки подшипника колесной пары для локомотива класса 294, модель, которая была введена в эксплуатацию в 1966 году. Оригинальная отливка имеет диаметр 374 мм, высоту 78 мм и весит 11,5 кг. Если крышка отсутствует, смазка может вытечь, что приведет к повреждению подшипника. В худшем случае это может привести к срыву локомотива.
Поставка заменяющего компонента для литейного производства займет до девяти месяцев, и в течение этого времени локомотив останется в нерабочем состоянии, что приводит к чрезмерно высоким затратам.
В рамках технико-экономического обоснования Deutsche Bahn разработала альтернативное решение с Rolf Lenk GmbH, средним бизнесом, специализирующимся на производстве добавок. В прошлом году Рольф Ленк приобрел станок Gefertec arc605, который работает с технологией 3DMP, аддитивным методом производства крупных компонентов на высокой скорости.
Дуговые аппараты Gefertec используют проволоку из металлического сплава в качестве сырья в процессе, сравнимом со сваркой, при этом слои материала накапливаются в форме готовой детали, имеющей почти чистую форму. Разработчик утверждает, что этот производственный процесс предлагает несколько преимуществ по сравнению с методами 3D-печати на основе порошка: 1) он устраняет необходимость в обработке порошка; и 2) большинство стандартных материалов легко доступны в форме проволоки по значительно более низкой цене, чем металлический порошок.
Самое большое преимущество, которое он заявляет, это высокая скорость наращивания — до 600 см3 в час, в зависимости от используемого материала. Это делает дуговой аппарат пригодным для быстрого и экономичного производства больших заготовок из стали, сплавов на основе никеля, титана или алюминия.
Дуговая машина доступна в 3-х осевой версии для заготовок объемом до 3 м3 ; 5-осевая версия для заготовок до 0,8 м3; и компактная 5-осевая версия для заготовок до 0,06 м3 .
Специально разработанное программное обеспечение CAM предоставляет данные CAD, детализирующие деталь, для создания данных ЧПУ, необходимых для позиционирования сварочной головки. Затем на станке Gefertec автоматически завершается изготовление заготовки, имеющей форму сетки. Отделка может быть выполнена с использованием обычного фрезерования с ЧПУ. Использование материалов в процессе 3DMP оптимизировано для снижения затрат по сравнению с другими производственными процессами, особенно для дорогостоящих материалов, таких как титан. В зависимости от применения производственные затраты могут быть снижены до 60%.
Данные САПР для деталей, используемых на старых рельсовых транспортных средствах, как правило, недоступны в цифровом формате, что означает, что для некоторых проектов Deutsche Bahn необходим полный процесс обратного проектирования. После завершения этого шага трехмерные данные должны быть обработаны для дугового аппарата Gefertec. Программное обеспечение 3DMP CAM, используемое для этой цели, генерирует специальные данные ЧПУ из цифровой модели детали. Затем дуговой аппарат приступает к формированию заготовки, как описано выше.
«Производство на машине Gefertec занимает всего около восьми часов, включая настройку», — объяснил Маттиас Отте, руководитель проекта в Rolf Lenk. После этого компонент почти чистой формы требует механической обработки. От первоначального проекта до реверс-инжиниринга и производства, проект был завершен в течение двух месяцев. «Это количество времени необходимо только для первого изготовления заготовки», — отметил Отте. «В зависимости от доступности оборудования, мы сможем произвести этот компонент через две-три недели».
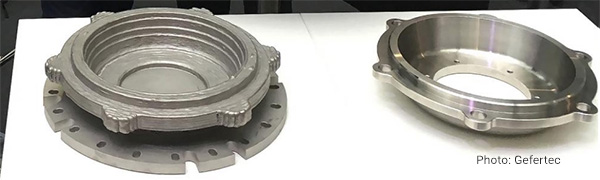
Рис. 2: Крышка подшипника колесной пары напечатана (слева) с использованием процесса 3DMP ® до почти чистой формы, а затем обработана (справа) до готового состояния
Готовая крышка подшипника колесной пары была тщательно протестирована Deutsche Bahn и в лаборатории материалов Федерального управления железных дорог Германии. «В дополнение к обычному анализу материаловедения, тестирование проводилось с использованием компьютерной томографии», — пояснил доктор Шлингманн. Постоянно положительные результаты подтверждают качество крышки подшипника колесной пары, полученной в процессе 3DMP. После завершения процесса сертификации для утверждения компонента для использования Deutsche Bahn деталь можно установить.
Цифровой склад запчастей — технико-экономическое обоснование использования аддитивного производства для крышки подшипника колесной пары — это только начало. Deutsche Bahn еще предстоит проделать работу по внедрению стандартного процесса поиска запасных частей. В качестве альтернативы эксплуатации сложных и дорогостоящих складов запасных частей складские помещения могут быть переведены в цифровую форму, так что все необходимые компоненты будут доступны в виде цифровых файлов. Затем детали можно изготавливать по мере необходимости на соответствующих станках для изготовления добавок. Наряду с улучшением доступности, эта концепция значительно снизит затраты не только на производство, но и на транспортировку и хранение.
Другим фактором является то, что критические компоненты должны быть утилизированы в конце срока их службы. Шлингманн также подчеркнул воздействие этого подхода на окружающую среду. «Каждый компонент поставляется с выбросом CO2, который может быть значительно сокращен при производстве добавок».
Источник: www.foundrymag.com
Tags:
3D печать