Главным пунктом продажи отливок по выплавляемым моделям всегда была точность — тонкие стенки, сложные формы и пустоты — и это вряд ли изменится для многих покупателей. Многие крупнейшие клиенты хотят получить точные детали в стабильных объемах, произведенные с помощью сертифицированных по качеству процессов, и часто из труднообрабатываемых материалов. Литейные цехи литейного производства имеют все это.
Но литье по выплавляемым моделям требует больше времени и опыта литейного производства, чем большинство процессов литья: точный прототип готовой детали формируется из воска. Эта модель, или несколько ее версий, припаивается к «дереву», которое затем погружается в керамическую суспензию и обсыпается огнеупором, который покрывает и затвердевает вокруг восковой формы. Эта последовательность повторяется до образования твердой керамической оболочки. Затем оболочки нагревают для выплавления восковой модели, оставляя пустая разогретая оболочка, в которую заливают расплавленный металл. Как только металл затвердевает, керамическая форма разрушается и отливка освобождается.
Это объяснение упрощено, и фактическая процедура может потребовать гораздо больших усилий. При обычном подходе производство от чертежа до готовой отливки может занять до 12 недель.
По словам Уолкера, инженера по продажам опытных образцов, Invest Cast — это литейный бизнес «в своей основе», но он также работает вверх по течению (быстрое прототипирование) и вниз по течению (чистовая обработка). Подразделение быстрого прототипирования использует 3D-принтеры для изготовления восковых моделей заказов клиентов, что приводит в движение процесс литья по выплавляемым моделям. «Благодаря 3D-печати весь процесс литья может быть выполнен всего за несколько дней».
Аддитивное производство (3D-печать) все еще кажется новым производственным процессом, но его применение в металлообработке хорошо известно. «Наш первый шаг к аддитивному производству произошел в 1999 году, когда наш генеральный директор обнаружил потенциал 3D-печатных моделей, которые могут быть отлиты в ускоренные сроки»», — объяснил Уолкер.
AM / 3DP описывает различные процессы, два из которых используются Invest Cast для поддержки операций по созданию прототипов: SLS (селективное лазерное спекание) для металлических деталей, SLA (стереолитография) для пластиковых рисунков и MJP (MultiJet Printing) для восковых моделей. «Эти технологии 3D-печати позволяют нам быстро создавать прототипы без изготовления оснастки для ускорения итераций проектирования», — сообщил Уолкер. «Интеграция аддитивного производства в наш рабочий процесс помогает нам более эффективно использовать наш опыт для наших клиентов».
Этими клиентами являются не просто крупные производители (аэрокосмическая, нефтегазодобывающая и перерабатывающая промышленность, сельскохозяйственное / внедорожное оборудование), но и «клиенты, которые просто ищут уникальную деталь, которую они разработали сами», отметил он.
«У нас есть персонал, который может удовлетворить любые потребности клиентов в отношении их литых деталей», — сказал Уолкер. «Мы можем провести обратный инжиниринг из самого грубого чертежа и в конечном итоге отправить вам отливку этого продукта. Наши штатные инженеры хорошо знакомы с процессом производства отливок по выплавляемым моделям, а также со всеми спецификациями и сторонними процессами, которые распространены в этой отрасли».
Первоначальной 3DP-системой Invest Cast был твердотельный принтер Thermojet от 3D Systems Inc. «Мы использовали его для клиентов, которые хотели небольших количеств, хотели их быстро или имели деталь, которая была, возможно, слишком сложной для литья с использованием традиционных инструментов».
В настоящее время Invest Cast эксплуатирует семь принтеров SLS, а также две последние модели 3D Systems для печати деталей воском — ProJet MJP 2500 IC. По словам менеджера по продукции Майка Норкитиса, он был представлен осенью прошлого года, основываясь на нескольких годах разработки и тестирования.
ProJet MJP 2500 IC основана на технологии MultiJet Printing 3D Systems для точного нанесения воскового рисунка (VisiJet ® M2 ICast) и поддерживающего воска (VisiJet ® M2 SUW) для создания трехмерной детали «слой за слоем».
«Два воска распыляются с помощью пьезоэлектрической печатающей головки, которая каждую секунду наносит десятки тысяч капель с каждого из 880 отдельных струй», — пояснил он. «Это позволяет очень быстро выполнять сборку, сохраняя при этом высокую точность». ProJet MJP 2500 имеет область построения 11,6 x 8,3 x 5,6 дюйма, с разрешением сборки 600 x 600 x 600 точек на дюйм, все в машинном конверте 44,1 x 29,1 x 42,1 дюйма.
«ProJet MJP 2500 IC адаптирован к потребностям индустрии литья по выплавляемым моделям для производства цифровых восковых моделей за долю времени, необходимого для создания традиционной оснастки для литья под давлением», — подчеркнул он.
«Цифровые восковые модели, создаваемые новыми принтерами 3D Systems, вписываются в существующий процесс воскового моделирования литейного производства без изменений», продолжил Норкитис. Это важно не только потому, что это ускоряет внедрение, но и потому, что оно делает литье по выплавляемым моделям некоторых отливок доступным, которые раньше они даже не могли рассматривать. «ProJet MJP 2500 IC откроет литейный завод для производства деталей, которые в настоящее время не формуются даже с растворимыми стержнями», — отметил он.
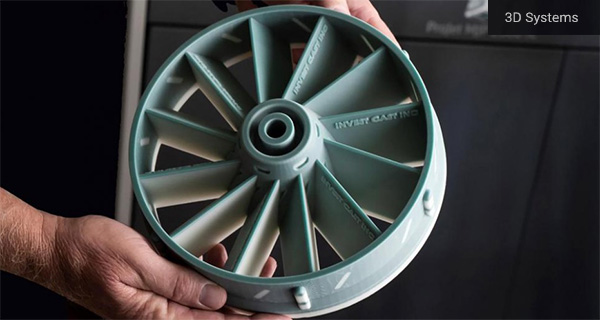
Восковая модель изготовленная на принтере ProJet ® MJP 2500 IC
Каждая установка включает в себя программное обеспечение 3D Systems 3D Sprint ® с функциями, разработанными специально для литейных цехов. «Invest Cast искал систему, которая могла бы производить модель литья по выплавляемым моделям с минимальными затратами времени», напомнил Уолкер. «Мы знали, что рынок существует, и нам просто нужны были машины для его поддержки». Через несколько месяцев после включения новых 3D-принтеров, Invest Cast обнаружил, что их ожидания были превышены. Он способен мгновенно преобразовывать данные CAD в восковые модели, готовые для использования в процессе литья.
В частности, было сокращено время выполнения точных отливок. «После того, как заказчик принял нашу заявку и мы получили заказ на покупку, мы немедленно отправили сборку одному из наших специалистов, который загрузит ее в один из IC-принтеров ProJet MJP 2500», — пояснил Уолкер. «Спустя несколько часов они вытащили сборку и доставить детали (литье по выплавляемым моделям) на наш завод в Миннеаполисе. Точно так же, через 5-10 дней, у клиента в руках отливки».
«Мы установили бета-установки на литейных заводах, чтобы обеспечить соответствие продукта и процессов конкретным потребностям индустрии литья по выплавляемым моделям», — рассказывает Норкитис. «В результате мы получили представление о том, как продукт будет использоваться в литейном производстве, и в дальнейшем разработали схему разреженного заполнения, которая позволяет изготавливать модели с содержанием строительного воска на 30% меньше, экономя деньги на литейном производстве на каждой модели»».
Благодаря доступным ProJet MJP 2500 IC, производителям литья по выплавляемым моделям не нужно производить технологическую оснастку для формирования восковых моделей, что, по словам разработчика, сокращает время поставки на несколько недель. Это также исключает затраты на инструмент и позволяет вносить больше изменений в конструкцию без очевидных затрат или времени, необходимых для модификации оснастки.
«Мы обнаруживаем, что ProJet MJP 2500 IC ориентированы на клиентов, которым необходимы более жесткие допуски, улучшенная обработка поверхности и более повторяемые отливки за небольшую долю времени производства», — заметил Уолкер из компании Cast Cast. «Меньшие и более замысловатые детали, кажется, являются хлебом с маслом для этих принтеров».
«Литейный завод, который внедрит в свой производственный процесс ProJet MJP 2500, получит возможность значительно быстрее поставлять готовые детали своим клиентам», — подчеркнул Норкитис. «Это позволит этим литейным предприятиям выполнять небольшие работы, которые ранее не были экономически эффективными, и получая при этом прибыль».
Источник: www.foundrymag.com
Tags:
ЛВМ