Обычный вопрос, который задают производителям шестерен их потенциальные клиенты: «Достаточно ли прочна эта шестерня для моего применения?» Без определителей этот вопрос в лучшем случае неоднозначен. Мировой рекорд в становой тяге составляет 536 кг (1181 фунт). Делает ли это рекордсмена достаточно сильным? Сможет ли он удержать этот вес 10 минут? Как насчет часа? Шестерня должна быть в состоянии выдерживать приложенный крутящий момент в течение желаемого срока службы шестерни. Таким образом, для ответа на ранее упомянутый вопрос о прочности необходимо учитывать прочность на изгиб и износостойкость поверхности.
Все металлы имеют прочность на изгиб, которая значительно выше, чем их поверхностная прочность или прочность на смятие. Чтобы повысить износостойкость поверхности и тем самым увеличить срок службы шестерни, шестерню можно подвергнуть термической обработке. Существует несколько способов термической обработки зубчатого колеса.
Закалка пламенем (рис. 1) является распространенным методом термической обработки зубьев шестерен. Он включает в себя использование горелки для нагрева определенных участков шестерни, обычно зубьев шестерни, для повышения долговечности поверхности. При ручном применении этот метод может дать неудовлетворительные результаты, поскольку время, затрачиваемое на нагрев каждой области, будет разным, расстояние, с которого применяется пламя, будет разным, и эти два варианта приведут к разной твердости поверхности шестерни. Даже когда процесс автоматизирован для устранения этих отклонений, зубчатое колесо все равно будет иметь некоторые искажения размеров, которые обычно снижают качество зубчатого колеса на один класс.
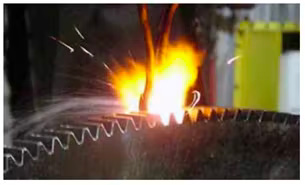
Рис. 1: Закалка пламенем.
KHK Gears USA, Inc.
Индукционная закалка (рис. 2) — еще один распространенный метод термической обработки зубчатых колес. В этом процессе шестерня окружена катушкой. Катушка находится под напряжением, создавая тем самым переменные магнитные поля. Эти поля, в свою очередь, генерируют вихревые токи, которые нагревают шестерню. Этот метод является довольно точным способом упрочнения всех зубьев шестерни до одинаковой твердости и глубины. Однако требуются определенные навыки и практика, чтобы определить время, необходимое каждой отдельной конфигурации зубчатого колеса для достижения желаемой твердости для конкретного материала. Одним из недостатков индукционной закалки является то, что области непосредственно рядом с зубьями шестерни также частично закалены. Это ограничивает доработку участков возле зубов после термической обработки.
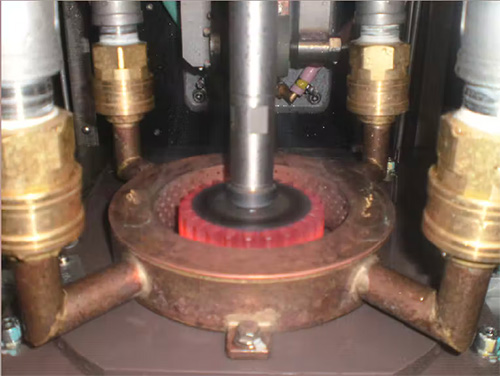
Рис. 2: Индукционная закалка
KHK Gears USA, Inc.
Третий метод термической обработки зубчатого колеса заключается в науглероживании зубчатого колеса (рис. 3 и рис. 4). Науглероживание — это процесс помещения шестерни в печь с добавлением углерода и нагрева печи до нескольких сотен градусов по Цельсию в течение длительного периода времени. Этот процесс позволяет добавленному углероду проникать в молекулярную структуру шестерни. Этот добавленный углерод приводит к образованию кожи из закаленного материала на самом внешнем слое шестерни.
В этом случае шестерня не может быть подвергнута повторной механической обработке после термической обработки, если только не используются твердосплавные инструменты или методы электроэрозионной обработки. Таким образом, желательно выполнять все операции механической обработки до науглероживания. Подобно индукционной закалке, для получения желаемых результатов при науглероживании требуется большое мастерство.
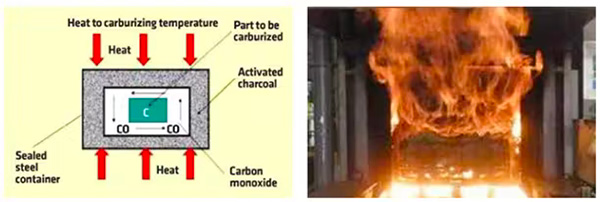
Слева: Рис. 3: Науглероживание; Справа: Рис. 4: Печь науглероживания.
KHK Gears USA, Inc.
Новейшим методом термообработки является лазерная закалка (рис. 5 а и б). Этот метод, как следует из названия, использует световую энергию для быстрого нагрева небольших участков зубчатого колеса. Он имеет ряд преимуществ перед всеми другими методами термической обработки. Первое преимущество заключается в том, что его можно использовать на очень небольших участках и не затрагивать близлежащие районы. Кроме того, поскольку он управляется ЧПУ, количество энергии, подаваемой на каждую секцию, идентично, а глубина твердости может быть ограничена. Так как импульс света применяется очень быстро, шестерня не имеет возможности нагреваться и, следовательно, не происходит ухудшения качества шестерни.
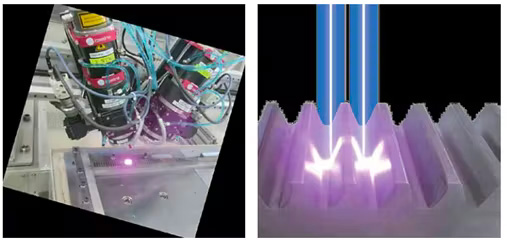
Слева Рис. 5а: Лазерное упрочнение; Справа Рис. 5б: Лазерное упрочнение.
KHK Gears USA, Inc.
Все методы термической обработки повышают прочность поверхности, но некоторые также снижают прочность на изгиб, так как материал после термической обработки становится хрупким. Ниже приведены некоторые примеры преимуществ термообработки:
-
-
- : Модуль 2, 15 зубьев, прямозубая шестерня из углеродистой стали 1045 с шириной передней поверхности 20 мм, имеет допустимый крутящий момент прочности на изгиб 29,6 Нм и поверхностную износостойкость 1,48 Нм. При индукционной закалке до твердости HRc 45-55 допустимый момент прочности на изгиб остается на уровне 29,6 Н·м, но прочность поверхности увеличивается до 10,5 Н·м. Это в 9 раз увеличивает прочность поверхности.
- : Модуль 2, 25 зубьев, прямозубая шестерня из углеродистой стали 1045 с шириной передней поверхности 20 мм, имеет допустимый крутящий момент прочности на изгиб 63,3 Нм и износостойкость поверхности 4,64 Нм. При индукционной закалке до твердости HRc 45-55 допустимый момент прочности на изгиб снижается до 52,7 Н·м, а поверхностная прочность увеличивается до 27,0 Н·м. Это увеличивает прочность поверхности в 5,8 раза и снижает прочность на изгиб на 16%.
- : Модуль 2, 40 зубьев, прямозубая шестерня из углеродистой стали 1045 с шириной передней поверхности 20 мм, имеет допустимый крутящий момент прочности на изгиб 118 Нм и износостойкость поверхности 12,5 Нм. При индукционной закалке до твердости HRc 45-55 допустимый момент прочности на изгиб снижается до 98,3 Н·м, а поверхностная прочность увеличивается до 72,1 Н·м. Это увеличивает прочность поверхности в 5,7 раза и снижает прочность на изгиб на 17%.
- : Модуль 2, зубчатая рейка из углеродистой стали 1045 с шириной торца 20 мм, имеет допустимую прочность на изгиб 3830 Н и поверхностную прочность 775 Н. При индукционной закалке до HRc 45-55 допустимый крутящий момент прочности на изгиб снижается до 3480 Н, но прочность поверхности увеличивается до 2000 Н. Это увеличение прочности поверхности в 2,5 раза и снижение прочности на изгиб на 9%. Однако при лазерной закалке до HRc 55-65 прочность на изгиб остается на уровне 3830 Н, а прочность поверхности увеличивается до 1730 Н. Это увеличение прочности поверхности в 2,2 раза без каких-либо искажений или снижения прочности на изгиб, которое происходит при использовании других методов.
-
Это лишь некоторые из многих способов термической обработки зубчатого колеса для повышения долговечности его поверхности. Каждый метод имеет свои преимущества и недостатки, но лазерная закалка является наиболее экономичным методом для закалки небольших партий.
Автор
Brian Dengel, генеральный директор KHK USA Inc
Источник: www.newequipment.com
Tags:
Термообработка